Engines, Tanks, Plant and Equipment Installations
Detail Oriented Craftsmanship We consider ourselves extremely fortunate in our extensive experience in catamaran design and construction. We therefore have an early understanding of what we need to emphasize at the initial stage of design and what needs to be incorporated into the design to achieve the best results, especially during the construction phase. Too often we see boats that display eye-catching style and craft, but are lacking in practical details. This is a mistake we resolutely decided not to make. Our focus went deep into the engine bay design to make sure we created a space that was as practical and efficient as the M37 deserved.
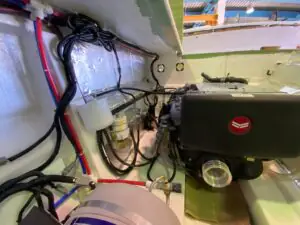
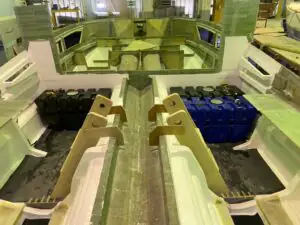
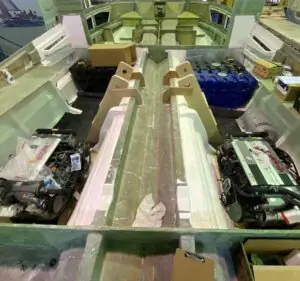
Engine Installation
We ignore the fact that this is a functional area and we believe that just as much effort and attention should be given to what is visible on the surface as to the hidden elements. It all starts with the engines; the two 370 horsepower V8 engines we have installed have great potential, but this power must be used effectively. It must transmit all the torque and horsepower through the substructure to the boat, turning it into forward momentum for the catamaran. It must also do so with minimal vibration and noise to the cockpit and cabins.
Strategic Placement to Reduce Noise
Before installing our tanks, we make sure that all areas of the engine area are painted white. While some builders may prefer a rough and unfinished approach, we believe that such an approach is inadequate for Makai. We chose white paint to create a bright, easily accessible and workable area. Then we start installing the three layers of soundproofing, which exceeds the standards usually used on boats of this size. We cover the main hull, the areas surrounding the engines and the entire top surface of the engine area, providing the best sound insulation for the cockpit and cabins. We meticulously planned the layout of the cabs, engines and tanks early in our design process and took a strategic approach to maximize the separation between the engines and sleeping areas. We also strategically positioned our tanks to create a liquid sound barrier between the engine and cabin area. Basically, if you are sleeping in the right-hand side hull, for example, there is a bathroom, sound insulation barrier, fuel tank and then a water tank to separate you and the engine. This creates a significant number of barriers so that sound does not pass through.
Water Tank Installation
After installing the insulation in hard-to-reach areas, we lift our specially manufactured polyethylene rotomolded tanks into place and secure them securely. These tanks have a capacity of 450 liters of fuel and 450 liters of water and are made with polyethylene material to prevent corrosion and block potential seam leaks. We designed them with thick walls, thus minimizing and effectively supporting the dynamic pressures caused by 450 kg of liquid circulating in harsh conditions.
Innovative Molded Infrastructure
We went through a lot of structural engineering literature before finally settling on an innovative molded substructure. This substructure provides rigidity and support for the hull where needed, as well as support and load transfer for the engines. We also include practical features such as flat floors for easy engine access and maintenance, support for mounting fuel and water tanks, and facilities for mounting electronics and hardware. We have also incorporated underground sump systems to keep your feet clean and dry when working around the engines. We have also separated the engine sump from other areas to prevent oily sump drainage that can harm the environment. All these improvements have been achieved through our vacuum injected engine grid substructure. By vacuum injecting and rigidly bonding these structures and covering them with glass, we achieve remarkable structural and practical improvements with minimal added weight. With the engine grilles firmly in place and our powerful V8 Yanmar engines installed, our engine rooms begin to take shape. However, these engines won’t go very far without fuel and they won’t perform optimally without adequate airflow. This is exactly what we are working on right now.
Engine Area Ventilation
Finally, once the engines, tanks, plumbing and equipment are all in place, we complete the engine zones by exposing the dorade vent with molded inlet. We have integrated this air intake into the window profile of the hull and have taken this approach to preserve the aesthetics of the hull. We have also extracted warm air from the stern of the vessel, supported by four centrifugal blowers. This high-flow airflow ensures that the engine rooms are well ventilated and operate at optimal temperatures, which significantly affects engine performance and fuel efficiency. Now that our engine rooms are fully equipped, the next important step will be the installation of our monocoque interior structure. Keep checking our stories page regularly for updates on our structure range or subscribe to our mailing list for progress updates.